Technology
Integrated packaging platform
All-in-one package: Combination of functionalities using scalable Wafer-Level Microfabrication techniques
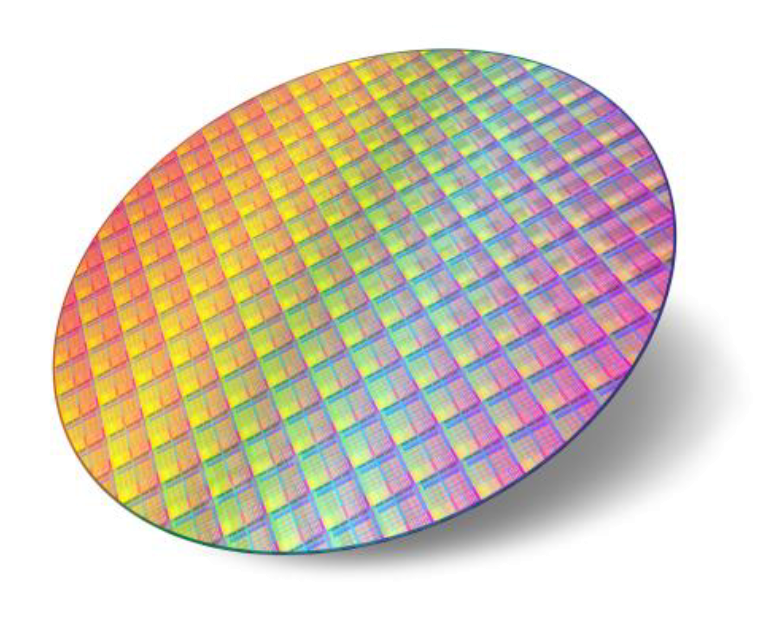
ICON brings a breaking through optical coupling technology allowing low-losses an easy assembly.
Easy fiber assembly using a mechanical fixture to provide fiber array self alignment in multiple fiber to chip configurations.
The wafer-level platform allows embedding the active chip devices in Si interposer such PIC, Detector, SNSPDs , VCSEL, LED, Laser, Electronics.
Integration and assembly of the previous functionalities in wafer-level.
Interposer also integrates high speed transmissions lines adapted to your active device.
Full on-wafer microoptics adding a extra beam control directly at the aperture level.
Our 3 main innovations
Optical coupling expertise
Being able to reach low losses (down to 0.1dB) at the components / fibers / waveguides optical interfaces as well as improving alignment tolerances (±30µm at 1dB of optical losses, in MultiMode usecase) is crucial for any system operations when continuous miniaturization is needed.
ICON Photonics has developed its expertise in this domain through years of development and patented technologies that enable a significant increase in systems coupling efficiencies. Our breaking-through light coupling is using polymer spot size converters, addressing both Multi-Mode and Single-Mode operations.
The technology is compatible with fiber arrays in both surface and edge coupling topologies.
Passive fiber
Improving the performances in a system already represents a high added-value. This added-value can however be enhanced by revamping the mechanical aspect of the fiber or ribbon fixtures.
ICON Photonics has developed solutions to integrate fiber fixtures adapted to the coupling structures already integrated on the chips or wafers, leading to high-performance self-alignment of large fiber ribbons (form x1 to x128 arrays).
The capability of high-volume industrialization is provided by our in-house wafer-level manufacturing processes, bringing precision (down to ±1µm) and scalability.
It finally results in cost-efficient solutions because of expensive assembly steps removing.
Si electrical interposer
Another important functionality proposed to you and given by our wafer-level manufacturing platform is the Silicon electrical interposer, custom-designed to embed your chip and to integrate ultra high-speed interconnections.
These lines can work up to more than 70GHz of bandwidth, enabling the next generation of high-speed optical sub-assemblies. The Silicon electrical interposer has been designed to be perfectly well integrated with both our optical coupling solutions and our passive fiber fixtures, but can also be provided alone.
All these solutions are compatible with standard processes such as wire-bonding or flip-chip techniques. It can always be adapted either for chip-level or wafer-level needs.
Adapted to your situation
Edge Coupling
Here you need to inject or collect light from a surface, either from / to a Photodiode, a VCSEL, a grating coupler (GC)… both at a chip-level or at a wafer-level.
ICON Photonics has worked on plenty of usecases to be able to answer all your surface coupling needs, with very high performances, and a very low cost of production.
Our proprietary coupling solutions are always adapted on-demand to fit with your chip situation, while passive fiber fixtures and Silicon electrical interposers can be added as options.
With pick-and-place processes or directly on your wafers, ICON Photonics will bring its added-value using standard photolithographic processes, compatible with all the production requirements.
Surface coupling
Here you need to inject or collect light from the chip edge, either from / to a DFB laser, waveguides…
This situation is critical since it is used in various industrial applications such as Telecom and PICs, where reducing the optical losses thanks to a better optical mode matching, as well as increasing the assembly alignment tolerances can have a huge impact on the final product value.
Using interposer techniques, ICON Photonics has developed a unique expertise to bring simultaneously very high optical and mechanical performances, always proposing our passive fiber fixtures and the Silicon electrical interposers as options.
But here, you keep an industrial production vision, all the structures still being produced at a wafer-level.
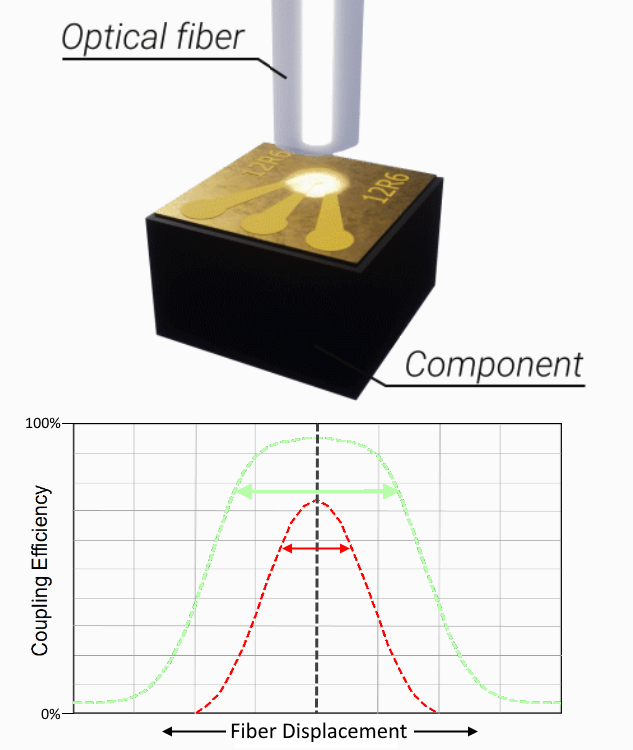
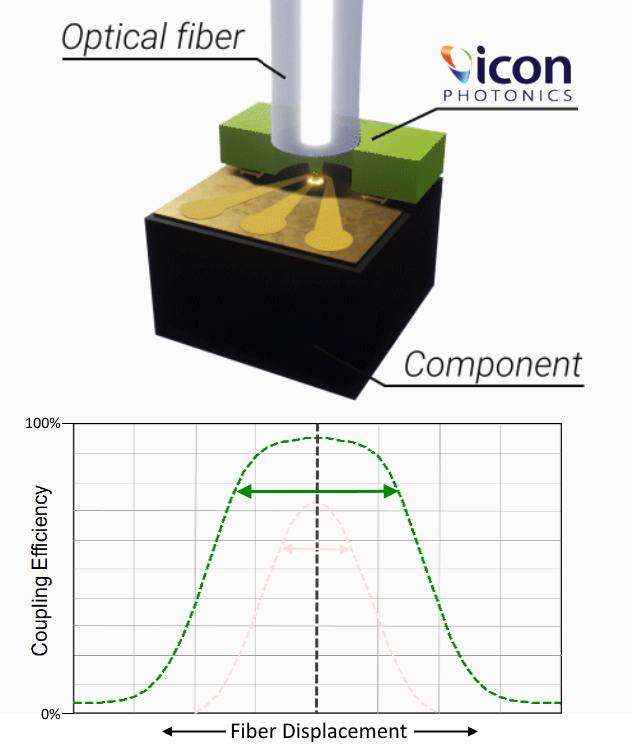
Others
At ICON Photonics we love all the coupling challenges and we know that all the “unusual” situations can be solved thanks to our unique expertises combination.
We can illustrate this with our multi-core fibers (MCF) coupling development, with the freespace situations (needed for LiDAR applications for example) where we shape the light beams directly at the chip / air interface, or with 90° turn solutions proposing an adpatation from an “edge” situation to a “surface” one and vice versa. All our different expertises can be mixed and used as services, our team being used to research & development.
Turning the unusual coupling situations to usual ones is clearly our motto here, always taking into account the final project vision, either being a small-volume one or a high-volume one.
Our 3 main innovations
Optical coupling expertise
Being able to reach low losses (down to 0.1dB) at the components / fibers / waveguides optical interfaces as well as improving alignment tolerances (±30µm at 1dB of optical losses, in MultiMode usecase) is crucial for any system operations when continuous miniaturization is needed.
ICON Photonics has developed its expertise in this domain through years of development and patented technologies that enable a significant increase in systems coupling efficiencies. Our breaking-through light coupling is using polymer spot size converters, addressing both Multi-Mode and Single-Mode operations.
The technology is compatible with fiber arrays in both surface and edge coupling topologies.
Passive fiber fixtures
Improving the performances in a system already represents a high added-value. This added-value can however be enhanced by revamping the mechanical aspect of the fiber or ribbon fixtures.
ICON Photonics has developed solutions to integrate fiber fixtures adapted to the coupling structures already integrated on the chips or wafers, leading to high-performance self-alignment of large fiber ribbons (form x1 to x128 arrays).
The capability of high-volume industrialization is provided by our in-house wafer-level manufacturing processes, bringing precision (down to ±1µm) and scalability.
It finally results in cost-efficient solutions because of expensive assembly steps removing.
Si electrical interposer
Another important functionality proposed to you and given by our wafer-level manufacturing platform is the Silicon electrical interposer, custom-designed to embed your chip and to integrate ultra high-speed interconnections.
These lines can work up to more than 70GHz of bandwidth, enabling the next generation of high-speed optical sub-assemblies. The Silicon electrical interposer has been designed to be perfectly well integrated with both our optical coupling solutions and our passive fiber fixtures, but can also be provided alone.
All these solutions are compatible with standard processes such as wire-bonding or flip-chip techniques. It can always be adapted either for chip-level or wafer-level needs.
Adapted to your situation
Surface packaging
Here you need to inject or collect light from a surface, either from / to a Photodiode, a VCSEL, a grating coupler (GC)… both at a chip-level or at a wafer-level.
ICON Photonics has worked on plenty of usecases to be able to answer all your surface coupling needs, with very high performances, and a very low cost of production.
Our proprietary coupling solutions are always adapted on-demand to fit with your chip situation, while passive fiber fixtures and Silicon electrical interposers can be added as options.
With pick-and-place processes or directly on your wafers, ICON Photonics will bring its added-value using standard photolithographic processes, compatible with all the production requirements.
Edge packaging
Here you need to inject or collect light from the chip edge, either from / to a DFB laser, waveguides…
This situation is critical since it is used in various industrial applications such as Telecom and PICs, where reducing the optical losses thanks to a better optical mode matching, as well as increasing the assembly alignment tolerances can have a huge impact on the final product value.
Using interposer techniques, ICON Photonics has developed a unique expertise to bring simultaneously very high optical and mechanical performances, always proposing our passive fiber fixtures and the Silicon electrical interposers as options.
But here, you keep an industrial production vision, all the structures still being produced at a wafer-level.
Others
At ICON Photonics we love all the coupling challenges and we know that all the “unusual” situations can be solved thanks to our unique expertises combination.
We can illustrate this with our multi-core fibers (MCF) coupling development, with the freespace situations (needed for LiDAR applications for example) where we shape the light beams directly at the chip / air interface, or with 90° turn solutions proposing an adpatation from an “edge” situation to a “surface” one and vice versa. All our different expertises can be mixed and used as services, our team being used to research & development.
Turning the unusual coupling situations to usual ones is clearly our motto here, always taking into account the final project vision, either being a small-volume one or a high-volume one.
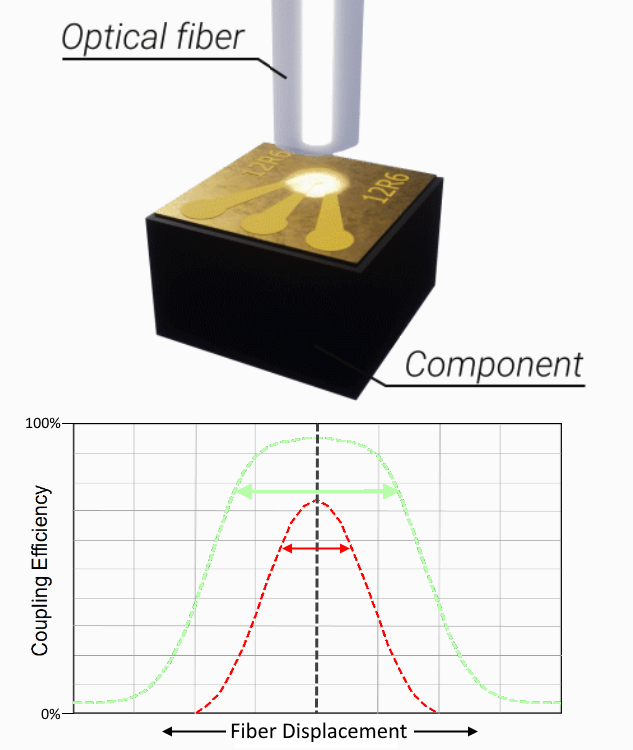
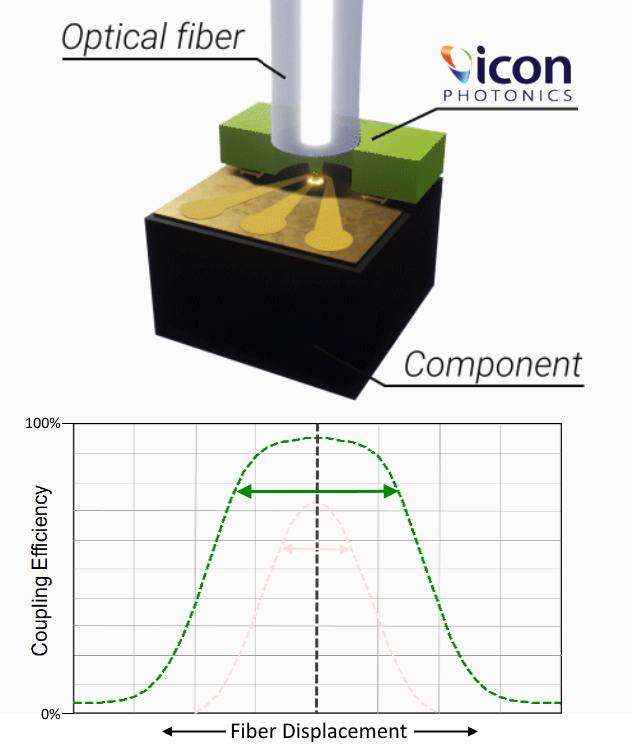


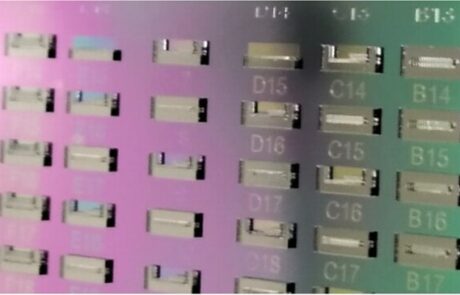
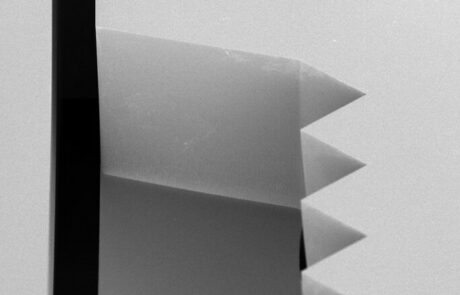
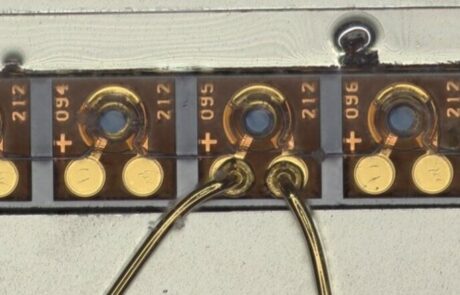
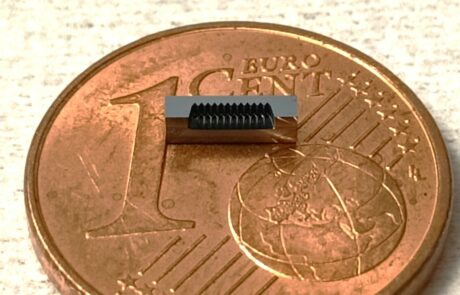
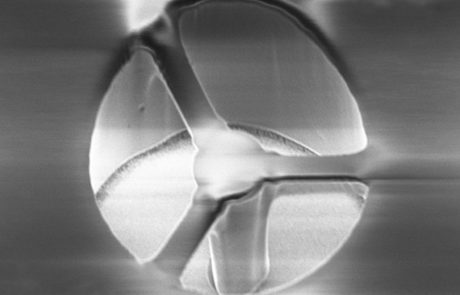

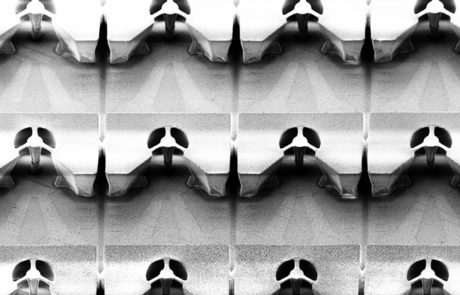
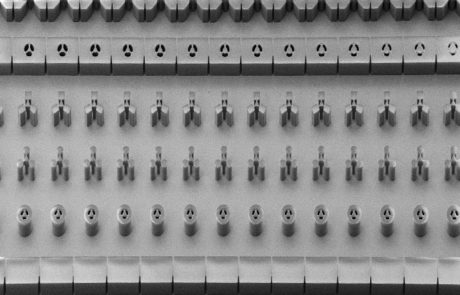
One technology. Multiple advantages.

MINIATURIZATION
Excellent precision by semiconductor processing techniques enabling low loss coupling and easy assembly process steps
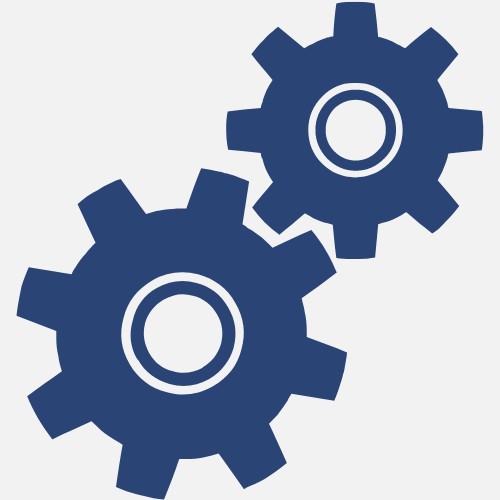
VERSATILITY
Easy customization applicable with multiple application : optical interconnects, quantum photonics, sensing
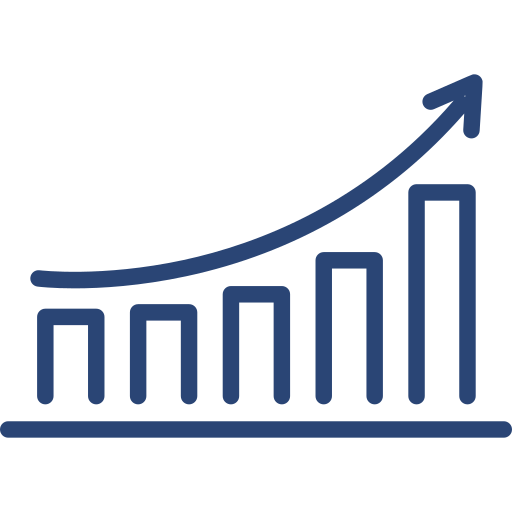
SCALABILITY
Wafer-Level microfabrication : cost-effective mass production solution
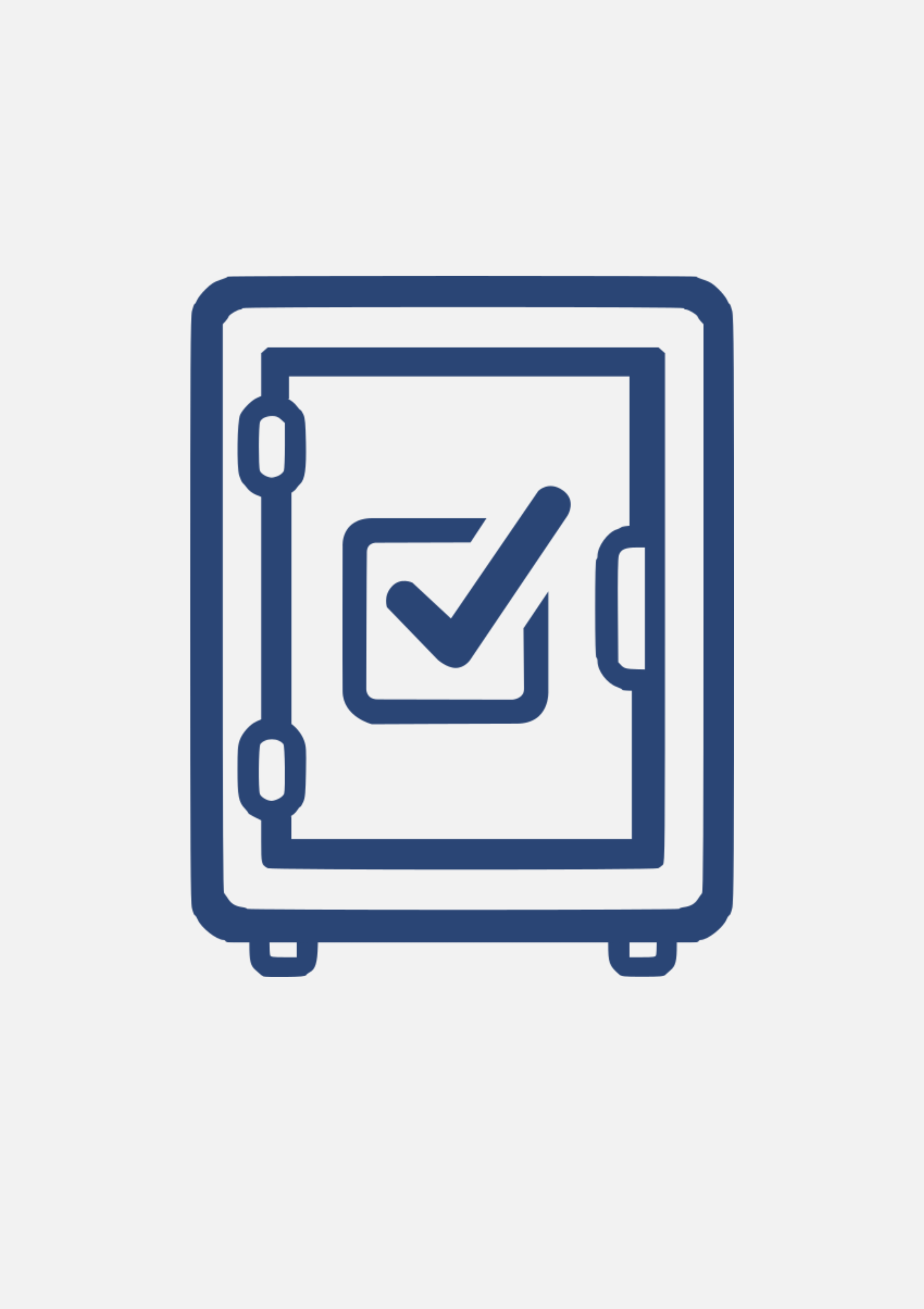
RELIABILITY
Survive from 4mK to more than 250°C: TELCORDIA standards passed
One cleanroom.
Many possibilities.
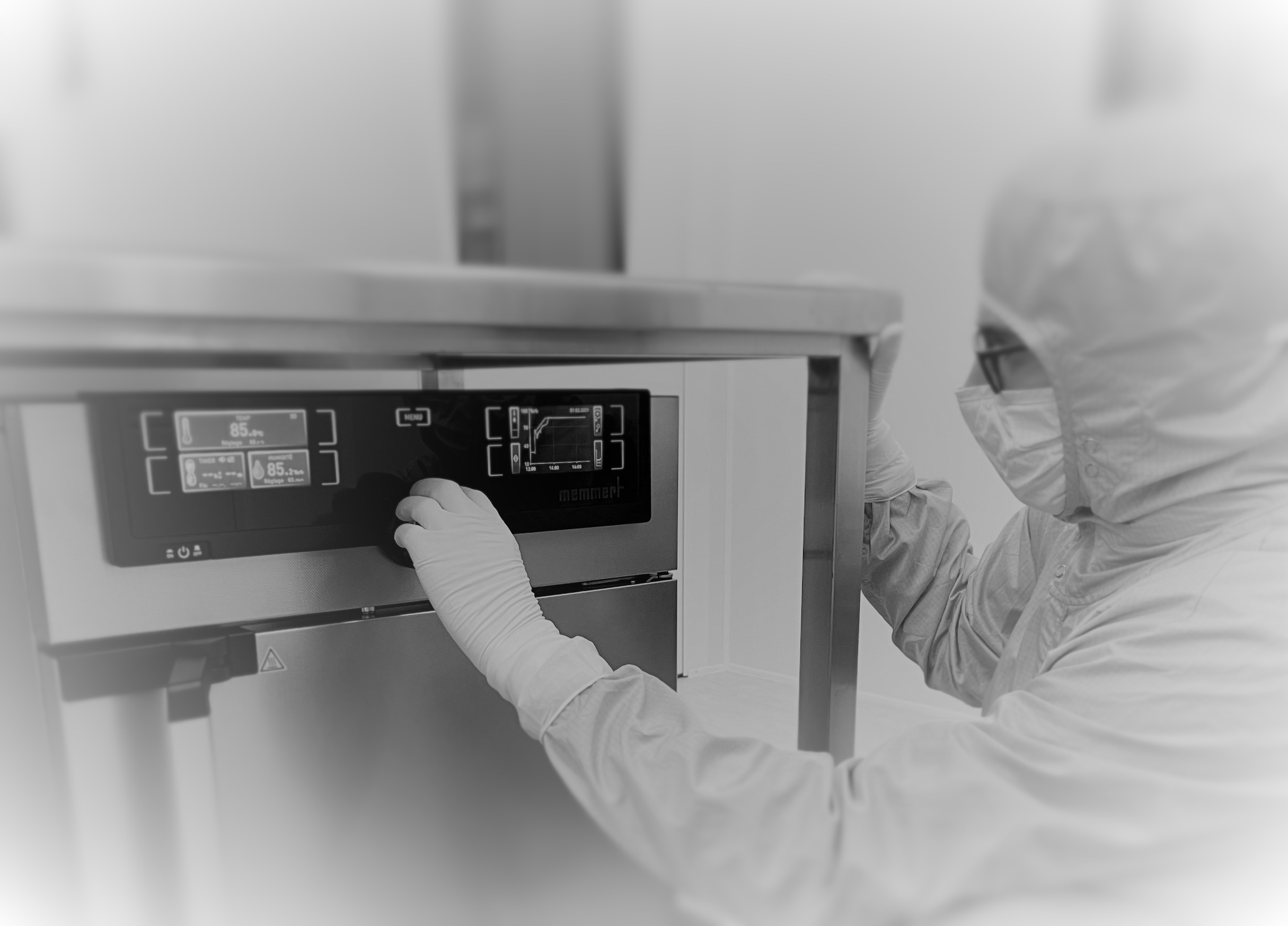
ICON Photonics can provide a wide variety of cleanroom services to suit your needs !
From backend to frontend process, ICON Photonics can provide the service you need. A few examples of our capabilities :
DRIE 3″ or 4″ or 6″, Dicing, Sputtering, Photolithography, Optical and mechanical profilometry, SEM characterization
As well as standard or custom reliability tests :
Temperature Cycling, Moisture, Shear stress, etc…